ASU Addresses Sustainability Goals With Novel Cement Technology
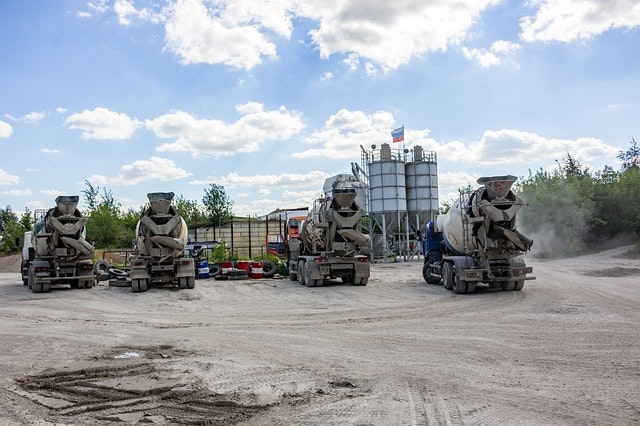
The project
Arizona State University’s Interdisciplinary Science and Technology 7 (ISTB-7) building is the latest among dozens of Leadership in Energy and Environmental Design (LEED) projects on campus and is, by far, its most ambitious.
ISTB-7 is a new, approximately 281,000 gross-square-foot, high-performance research facility that fosters an interdisciplinary approach to knowledge generation and leading-edge research, including innovative endeavors focusing on the sustainability of food, water, and energy.
In expanding the research district at ASU’s Tempe campus, the building will give researchers a means to collaborate on pressing environmental and food-related challenges. In addition to offering public outreach and exhibit space, ISTB-7 will be home to the Julie Ann Wrigley Global Futures Laboratory, the Rob and Melani Walton Sustainability Solutions Service, the School of Sustainability, the Institute of Human Origins, and a five-story courtyard biome of flora and fauna.
Using a range of innovative approaches, including evapotranspiration, photovoltaics, and ASU’s own carbon-capture technology, the building is pursuing LEED Platinum status. The ISTB-7 building, when completed, will support and demonstrate research advancing sustainability. Yet, according to a statement from ASU, “It is important that the actual structure delivers and inspires sustainability, as well.”
The challenge
Cement is carbon-intensive to produce, so reducing the amount of cement in the building’s concrete mix was a priority for lowering the project’s embodied carbon footprint. The team set out to utilize a post-consumer byproduct to reduce the total amount of Portland cement in the building structure by at least 40%. “It takes a lot of equipment and resources to produce cement,” said McCarthy Building Companies’ Senior Project Manager Carlos Diaz. “If you can replace a high percentage of cement with a recycled material like fly ash, you can offset a significant amount of carbon.”
In addition to the high criteria sustainability requirements, the concrete needed to be aesthetically pleasing, since it would be used in Class A architecturally exposed columns, walls, stairs, deck soffits, and polished concrete floors.
The solution
Ready-mix producer Hanson Aggregates LLC (a subsidiary of Lehigh Hanson), concrete contractor McCarthy Building Companies, and admixture supplier GCP Applied Technologies worked closely together to identify the right concrete mix that could substantially reduce the amount of cement required for construction, thus improving sustainability. The firms bring together significant expertise in helping customers improve building durability and reduce waste.
Lehigh Hanson/Hanson Aggregates advocate for science-based research that drives innovation and sustainable building design. Named one of the top 20 green builders in the country, McCarthy Building Companies is deeply involved in the evolution of sustainable construction. And GCP Applied Technologies specializes in developing products that make the manufacture of construction materials such as concrete more energy efficient.
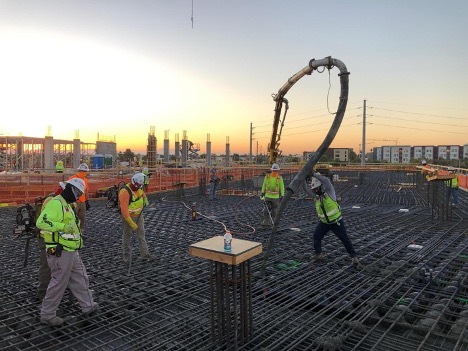
Achieving the right concrete mix was no simple task. Although 40 percent cement-replacement mixes are not uncommon, they are typically usually used in a targeted approach, such as to control the heat of hydration. With this project, the mix would need to be applied whole-scale throughout the entire building.
“Ready-mix concrete is sometimes viewed as a commodity, but the delivery of a product that has a widescale application – especially one with architectural aspects to it – requires a significant mind shift,” said Diaz. “It takes months to determine the right mix – making sure the suppliers and chemical partners are working together to find the best admixtures, color, and supplementary cementitious material (SCM) for the application.”
McCarthy Building Companies’ Senior Project Engineer Kristine Sorensen confirms the considerable effort that went into cement development: “There was a great deal of collaboration involved with identifying a sustainable mix design that would meet the structural integrity measures and would also look outstanding,” she said.
“Everyone involved in the project came together to discuss different mix design scenarios and how to use locally available resources,” said Hanson Aggregates’ Quality Control Manager Joel Lopez Martinez. “Using high fly ash mix design for the 6,000 PSI mix is beneficial, as it reduces permeability to water and produces a densified product.”
“Many times, we have a pool of ready-mix contractors to work with and they have lots of mix designs already predetermined based on a project’s mix, strength, and flowability requirements,” said Diaz. “When you’re creating something new with high-strength requirements like this, there’s a big team effort required. Together, we gathered input from the design team and then looked at all aspects of the job to answer questions such as, ‘How do you control heat?’ and ‘How will the mix flow through congested rebar?’”
For this mix, Hanson Aggregates used fly ash, along with WRDA 64® water reducer with ADVA® 195 superplasticizer from GCP Applied Technologies. Once they selected a mix, the team started batch trials to ensure it performed as structurally intended. Based on the success of those results, they finalized the mix and began the concrete pour.
“The ADVA® admixture gave us the opportunity to keep the water/cement ratio low while achieving high strength, as well as the workability to place the concrete very easily,” said Bill Wheeler, Quality Control for Hanson Aggregates. “We prefer using the ADVA® admixture because it results in fewer bubbles against the surface than mid-range water reducers. This creates a smoother finish on the forms.”
[caption id="attachment_1042713" align="aligncenter" width="468"] The team’s innovative approach extended to its application of concrete. Using a patented BubbleDeck design linking air, steel, and concrete in structural slabs, they reduced the amount of structural concrete needed on decks 2, 3, 4, 5, and 6. Photo courtesy of McCarthy Building Companies.
By all accounts, the project has proceeded smoothly and is slated for completion in December 2021. “This is a legacy building that tells a unique story,” Diaz said. “We’re privileged to be a part of it.”
Project credits and technical details
Architect/Designer: Architekton | Grimshaw
Structural Engineer: BuroHappold
Sustainability Consultant: Thornton Tomasetti
Ready-mix Producer: Hanson Aggregates LLC. (a subsidiary of Lehigh Hanson, Inc.)
Concrete Contractor: McCarthy Building Companies, Inc.
GCP Solutions: WRDA® 64 water-reducing admixture, ADVA® 195 high-range admixture
Concrete mix and specifications:
- 4,000 PSI for slab on grade, grade beams, caissons, caisson caps, and foundation walls; 5,000 PSI for shear walls and stairs; 6,000 PSI for elevated slabs; and 8,000 PSI for columns
- SCM: Class F fly ash
- Aggregate: One-inch rock
Volume: 16,000 total cubic yards
[caption id="attachment_1042723" align="aligncenter" width="281"] BubbleDeck designs involve inserting hollow plastic balls into the slab and holding them in place with steel reinforcement. The plastic balls would normally be filled with concrete. This design approach enabled lighter decks so the column spacing is wider. Photo courtesy of McCarthy Building Companies.
About the author
Lisa Barnard, CSI, LEED AP O+M, WELL AP is a GCP Account Manager for Concrete Admixtures and VERIFI® In-transit Concrete Management System. In addition to her sales role, she also brings her expertise to marketing, communications, and EHS around corporate sustainability issues, LCA, EPD, UN Sustainable Development Goals, and green building standards/certification programs. She currently serves as the Technical Committee Chair for the CSI Phoenix Chapter and the Market Advisory board for USGBC AZ.