Vector manufacturing for cell and gene therapies: how should current platforms be changed?
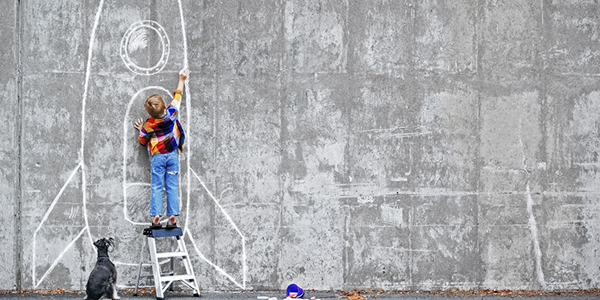
As the demand for vectors in the [cell and gene therapies] space grows, where do the biggest changes need to be made with regards to current manufacturing platforms?
In a recent study by Informa Connect on the challenges of using vectors in producing cell and gene therapeutic products, this open question received many different responses from biotech professionals in the field across North America and Europe.
However, the most common answer was scalability. The suggestions ranged from ‘scalability on same platform to enable rapid scale up from lab to commercial supply’and ‘scalable flexible manufacturing platforms are necessary’ to ‘scale up of animal free high quality component’. Other common answers included switching to non-viral vector solutions, GMP compliance, improved yield, higher titers and industrial standardization.
The responses included:
- “Yield, large scale and rapid manufacturing, turnaround time for autologous therapeutic products”
- “Better tools for purification and characterization of vectors”
- “Process efficiency and robustness need a quantum leap. Current processes are clunky, expensive and unreliable”
- “True scaling up with AAV rather than scaling "out"”
- “Lack of coordinated and standardization of processes for intellectual property considerations. The field is evolving from a less populated/collaborative approach to a more crowded/competitive mindset with its growth.”
- “We are currently switching to non-viral DNA delivery systems. The manufacturing of vectors is becoming cost-prohibitive for us to do ourselves and also to purchase from other vendors”
- “Clarity on allowable use of animal derived components such as FBS”
- “More stable cell lines- need for less complicated plasmid process where possible process intensification- to suspension platforms (linked to point 1) reduction in COGs also ensuring high purification yields and less freeze/thaw losses”
- “Small footprint, flexibility and analytics”
- “Higher titres/downstream; flexible cell lines; inline monitoring re. CQAs - real time release”
- “The viral vector production should be manufactured only in GMP approved site”
- “Size and number of genes each vector can carry”
The survey respondents were also asked what the biggest pain point is in scaling up viral vector manufacturing for commercialization and which emerging tools are most greatly needed for vector characterization.