Cement Solutions: Balancing Sustainability, Savings, and Strength
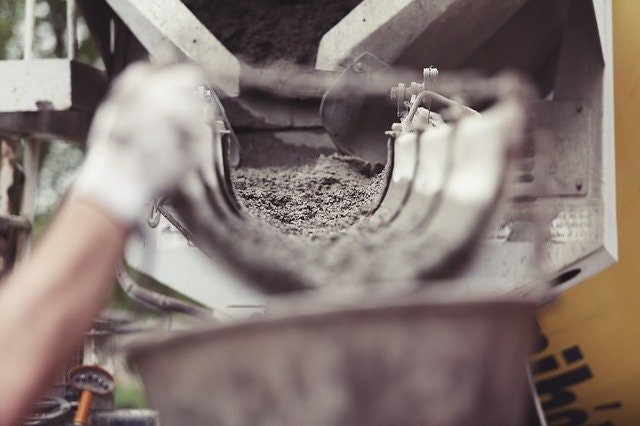
The news is filled with promising reports of cement producers pursuing carbon-neutral solutions. However, there has been considerably less discussion of the myriad challenges producers face as they work towards achieving this goal.
Although there are exciting solutions available today to curb CO² emissions, implementing them requires multiple considerations to ensure they are maximizing value at all stages of the supply chain.
Investors driving climate action
Producers are under considerable pressure to produce cement in a more sustainable way. For example, members of the Institutional Investors Group on Climate Change and Climate Action 100+, a coalition of money managers with more than $33 trillion under management, are urging European construction-material companies – including cement makers – to commit to reducing net CO² emissions to zero by 2050. Furthermore, investment group member and CEO of Ethos Foundation Vincent Kaufmann has noted that "an increasing number of investors seek to exclude highly carbon-intensive sectors from their portfolios to meet their decarbonization plans."
In an annual letter to CEOs, asset management powerhouse Blackrock Inc. announced that climate change has become a defining factor in evaluating companies’ long-term viability, noting that, “over time, companies and countries that do not respond to stakeholders and address sustainability risks will encounter growing skepticism from the markets, and in turn, a higher cost of capital.”
As the world's largest asset manager, with approximately $8.6 trillion in assets, Blackrock has introduced numerous initiatives that place sustainability at the center of its investment approach, including making sustainability integral to portfolio construction and risk management; exiting investments that present a high sustainability-related risk (such as thermal coal producers); launching new investment products that screen fossil fuels; and strengthening its commitment to sustainability and transparency in its investment stewardship activities.
Tying sustainability and strength
Despite these mounting pressures, it has not been easy for the cement industry to make immediate adjustments. Given that their building materials are expected to last for generations, producers are understandably wary of making changes without full assurance that they will not negatively impact the integrity of their product. In other words, sustainability products must preserve the strength and other desirable performance properties of the cement before producers will consider using them.
Fortunately, there are a number of solutions – both chemical and technical – that are enabling producers to do just that. However, there are no one-size-fits-all solutions here. Each plant needs to take a holistic view of conditions in order to identify the best approach, which may encompass:
- Conducting lab tests to identify custom chemistries for specific cement and concrete systems
- Enhancing the efficiency of the ball mill or vertical mill
- Ensuring best-in-class execution during field trials and regular operations.
Here’s an example: A cement plant customer in eastern Europe recently sought a grinding additive to facilitate a further 4% clinker replacement for their cement above the 3% reduction they were already achieving with a traditional GCP Applied Technologies quality improver. GCP designed the new product, tested it on site, and produced cement of the same fineness. The resulting strength was increased in the order of 10% at all ages, in addition to achieving an increase in cement mill output of more than 4%. This enabled the plant to:
- Reduce clinker by the desired 4% by increasing the limestone content
- Reduce operational costs by over 2%
- Lower CO² emissions by a further 6% on top of previous additives.
Capitalizing on new market opportunities
Estimated to account for 7% of global man-made CO² emissions, cement is under the microscope when it comes to improving sustainability. Although there are goals such as the International Energy Agency’s Sustainable Development Scenario to drive incremental change, it is likely that market opportunities are what will spur the industry forward. For example, the green cement market is estimated to grow to $43.59 billion by 2027, providing a wealth of opportunities for producers who capitalize on these shifts.
Fortunately, there are effective ways to help reduce embodied carbon in cement today through chemical cement additives. For instance, cement additive technologies first developed and introduced by GCP are currently enabling the cement industry to reduce approximately 65 million tons of CO² per year. That represents roughly three percent of global cement CO² emissions.¹
Accelerating the selection of sustainable additives
Using multiple chemicals together can often offer sustainability advantages that represent more than the sum of their parts. However, with so many cement chemistries and variables to choose from, not to mention individual constraints in each cement, it can be difficult for cement plants to readily predict the performance of multiple chemistries working together.
Accurately predicting the anticipated strength and sustainability benefits involves a careful assessment of the existing business and technical needs and constraints. Having these discussions with your additive supplier can help to reliably increase the use of supplementary cementitious materials to reduce the carbon footprint and identify formulations that offer an improved net value.
Conclusion
Reducing CO² is a critical endeavor for cement plants. Choosing the right solutions involves a keen understanding of individual market conditions, the availability of locally sourced raw materials, cement performance goals and metrics, and predictors of chemical additives. Working in partnership with cement plants to understand specific objectives and operational processes can help drive decisions that result in the trifecta of sustainability, strength, and savings.
¹One-year carbon emission reduction, on the basis of 2019 volumes
About the Author
Riccardo Stoppa is the Global Marketing Manager of the Cement Additives division at GCP Applied Technologies. He holds a master’s degree in industrial chemistry from the University of Milan and an MBA from the SDA Bocconi School of Management. Riccardo has contributed to the development and launch of new technologies and products such as the CO2ST® reducer, Tavero® VM, and innovative services such as the GCP DASH® real-time product selection application. The company takes a holistic approach to tackling CO² reduction, bringing together chemical research, experienced technical support, lab and field testing, advanced chemistry, and technology to ensure that new chemistries they develop bring strength, savings, and sustainability to customers.